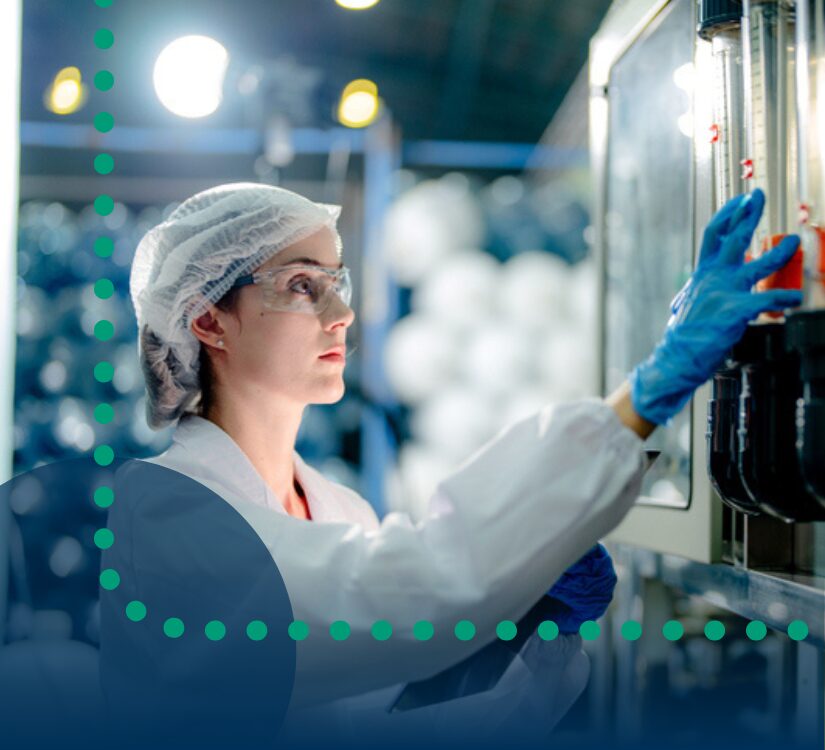
In the rapidly evolving medical manufacturing landscape, one challenge stands paramount: maintaining rigorous safety standards while fostering innovation. The balancing act between compliance and advancement isn’t just about checking boxes—it’s about creating a framework where innovation can thrive without compromising patient safety.
Here’s how successful medical manufacturers are navigating this complex terrain.
The real price of compliance
The cost of regulatory compliance extends far beyond direct expenses. While companies must invest in quality management systems and documentation processes, the reality is more complex than simple line items on a budget.
Extended development timelines often result in increased labor costs and delayed market entry. Testing requirements compound these delays, requiring extensive validation processes and documentation. Regular audits and inspections demand dedicated personnel and resources, while employee training and certification programs require ongoing investment.
Perhaps most significantly, documentation management systems—though essential—require substantial investment in both technology and personnel. However, viewing these as mere expenses rather than investments can be shortsighted.
Innovation within boundaries
Contrary to popular belief, regulatory frameworks don’t always stifle innovation. Smart manufacturers are discovering that compliance can actually drive creative problem-solving and advancement. By integrating compliance requirements early in the design phase, companies can avoid costly retrofitting and ensure smoother product launches.
Risk-based approaches to validation processes have emerged as a powerful tool, allowing manufacturers to focus resources where they matter most. This strategic approach not only ensures compliance but often leads to more efficient processes overall.
Technology as a compliance partner
Digital transformation is revolutionizing how manufacturers approach compliance. AI-powered quality control systems are now capable of predicting potential issues before they become problems, dramatically reducing the risk of non-compliance while speeding up production.
Cloud-based documentation management enables real-time updates and instant access to critical information across global operations. Digital twins have become invaluable tools for testing innovations without risking compliance violations, allowing manufacturers to experiment safely in virtual environments.
Automated audit trails have significantly reduced human error while providing unprecedented visibility into manufacturing processes. This technology not only ensures compliance but often identifies opportunities for process improvement.
The human factor
At the heart of successful compliance programs lies the human element. Building a culture of compliance isn’t just about rules and regulations—it’s about creating an environment where every employee understands their role in maintaining quality and safety.
Regular training and skill development programs ensure that staff remain current with the latest requirements and best practices. Clear communication channels help ensure that compliance requirements are understood and followed at every level of the organization.
Employee engagement in improvement processes has proven crucial for identifying potential issues early and developing innovative solutions. When staff feel empowered to contribute to compliance efforts, they become active participants in maintaining safety while driving innovation.
A trusted partner like Staff Management can help you build an effective and safe medical manufacturing workforce.
Global considerations
In an interconnected world, manufacturers must navigate a complex web of regulatory frameworks. FDA requirements in the United States often differ from EU MDR compliance standards in Europe, while Asian markets present their own unique challenges. Emerging markets add another layer of complexity with rapidly evolving regulatory requirements.
This global perspective requires a robust and adaptable compliance strategy that can accommodate regional variations while maintaining consistent quality standards across operations.
Finding the sweet spot
The key to balancing safety and innovation lies in viewing compliance not as a barrier but as a framework for sustainable innovation. By integrating compliance considerations early in the development process, manufacturers can reduce costly redesigns and speed up time-to-market while building customer trust.
This approach leads to more reliable products and drives continuous improvement across the organization. The most successful manufacturers have learned that compliance and innovation aren’t opposing forces—they’re complementary elements of a successful operation.
The future of compliant innovation
As technology evolves and regulatory frameworks mature, successful manufacturers will be those who can adapt quickly to changing requirements while maintaining robust quality systems. The future belongs to organizations that can leverage new technologies for compliance while fostering a culture of innovative compliance.
In the end, the cost of compliance should be measured not just in dollars spent, but in the value created through safer, more innovative medical products. The most successful manufacturers understand that investing in compliance today paves the way for innovation tomorrow.
With over 10 years of experience, we at Staff Management | SMX know the medical and pharmaceutical industry inside and out. Explore our medical and pharmaceutical industry expertise by checking out our info sheet and contact our team today to learn more about our medical and pharmaceutical solutions.