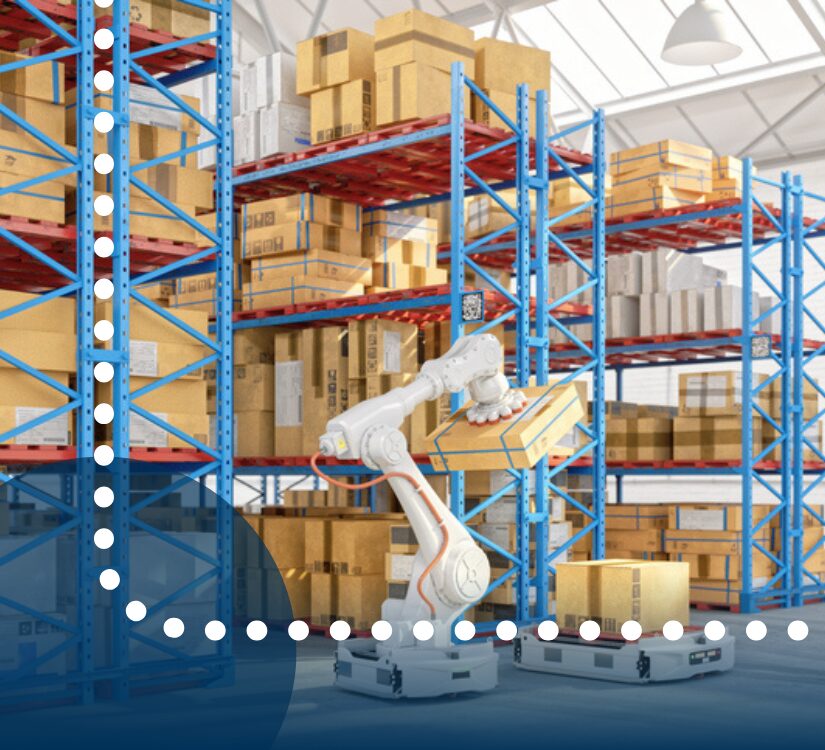
Artificial intelligence, more commonly referred to as AI, is a hot topic for warehouse operation leaders. Simply put, AI is a computer system that mimics human intelligence in areas like translation, speech recognition and decision making without the need for much human interaction.
On one end of the spectrum, there are advanced AI systems, like cognitive computing, that can learn and acquire new skills. These systems include driverless cars or autonomous robots that don’t require total human control. Alternatively, there are simpler and less sophisticated forms of AI like voice-enabled speakers.
AI includes a few different technologies suitable for warehouse operations that improve picking and inventory accuracy and reorganize data to support decision making and accelerate the order fulfillment process.
Here are three types of AI commonly utilized to boost productivity and efficiency in distribution and fulfillment centers today.
1. Machine Learning
Aside from being used in spam filtration and voice-activated assistants, machine learning takes the massive amount of data collected in a warehouse, like inventory and order numbers, and quickly translates it into actionable language. It “learns” from the data using algorithms, and it reports insights without being directly programmed on how to find them. This type of AI has the ability to identify inventory and order patterns to reveal which items are selling and should be restocked first.
Machine learning can also analyze and report consumer demand by interpreting data based on orders and returns. This reduces operating costs by cutting wasted replenishment and can improve customer service because its accuracy will show actual on-hand inventory. Cloud-based analytics provider FusionOps suggests that machine learning can improve demand forecast accuracy by more than 20 percent.
2. Speech Recognition
Voice-picking technology is not new to fulfillment operations but recent AI improvements have enhanced its capabilities. Utilizing this technology has been shown to reduce picking errors by up to 90 percent.
Ongoing advancements have blended speech recognition, a form of AI, with the older voice-picking technology, which improves picking accuracy and speed. Associates wear a headset and microphone that is connected to the warehouse management system (WMS). The WMS gives the worker instructions through the headset like what item to pick and where it’s located. The worker then reads the item’s number when it’s found, and using speech recognition, the system recognizes the worker’s voice and confirms the picked item.
The system is “trained” to learn the worker’s tone and speech patterns the more it’s used and allows the associate to work hands-free and more safely.
The video below shows voice-picking technology in use. The system guides the worker to the correct location in the warehouse and tells her what items to pick. The associate confirms the item by repeating the number and quantity back.
How will this technology evolve next? Some pick programs are now incorporating visual headsets that make use of augmented reality to further increase efficiency.
3. Cognitive Robotics
Robotics are becoming a part of fulfillment operations more quickly than originally expected. Nearly 40,000 robotics were shipped to warehouses in 2016, but market intelligence firm Tractica predicts that amount will jump to 620,000 in four years.
Robotic technology comes in varying levels of sophistication and aren’t as far-fetched as some people would think. Some are limited to unloading or pallet stacking while others are capable of picking orders and delivering them to workers. AI is more noticeable in the latter because they are able to maneuver across the warehouse floor with limited human interaction and can self-adjust depending on their surroundings.
Not surprisingly, Amazon operates the largest line of industrial robotics with 45,000 deployed throughout its fulfillment centers, but this technology is not out of reach for midsize companies.
Men’s fashion etailer Bonobos and its partnering fulfillment center use robotic technology to quickly find items to package and ship. An item can be found as soon as an order is placed boosting productivity by 800 percent. If you’re considering deploying industrial robots, make sure that you’re protected from vulnerabilities that could provide a back door for hackers.
Integrating AI in Your Operation
Artificial intelligence is expanding rapidly into fulfillment and distribution centers at a time when online orders are rising and quick deliveries are a must. Large companies like Amazon, Walmart and Target have the resources to implement highly sophisticated AI in their operations, but that doesn’t mean midsize companies should be discouraged. AI is becoming more accessible as advancements become more broadly available. Mike Jackson, CEO and president of Pendello Solutions, a company that provides technology management to small and midsize businesses, suggests that most small businesses should partner with third-party technology suppliers at the beginning rather than create in-house AI and machine-learning solutions to save money.
Although there have been concerns of artificial intelligence taking over these types of operations, AI will likely function collaboratively with human workers. Companies will still need associates to operate the AI systems, ensure accuracy and pack orders. For example, Amazon’s hiring rate hasn’t changed much despite increasing their use of robotics. Ultimately, AI helps improve accuracy and create a more productive and faster workforce instead of replacing it.
Integrating artificial intelligence is only one way your fulfillment operation will soon change. Discover other fulfillment center transformations in our 2017 Fulfillment Trends Infographic >