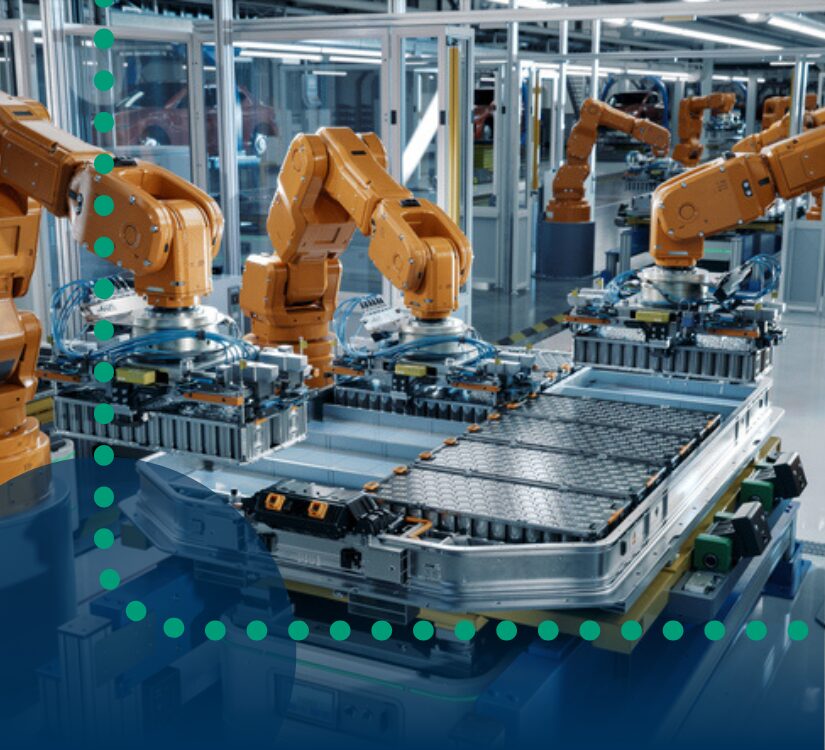
The electric vehicle (EV) manufacturing landscape is undergoing a revolutionary transformation, driven by technological innovations, evolving market demands and increasingly stringent regulatory frameworks.
Let’s examine the key trends reshaping the industry’s future.
Manufacturing innovation
The manufacturing process for electric vehicles is experiencing a shift towards advanced automation and digital integration. Gigafactories are increasingly implementing lights-out manufacturing systems, where production continues 24/7 with minimal human intervention.
Advanced robotics systems, coupled with AI-driven quality control mechanisms, are becoming the industry standard, dramatically reducing error rates and improving consistency in production.
Digital twin technology has emerged as a crucial tool in modern EV manufacturing. These virtual replicas of production lines enable real-time monitoring, optimization, and predictive maintenance, significantly reducing downtime and improving overall efficiency.
Manufacturers are using these digital twins to simulate and optimize production processes before implementing changes in the physical world, resulting in substantial cost savings and reduced risk in process modifications.
Battery technology advancement
Battery technology continues to be the primary focus of innovation in the EV sector. Solid-state batteries are beginning to enter limited production, representing a significant leap forward in energy storage technology.
These batteries offer higher energy density, faster charging capabilities, and enhanced safety profiles compared to traditional lithium-ion batteries. The transition to solid-state technology is expected to reduce production costs while simultaneously improving vehicle performance.
The industry is witnessing a fundamental shift in cathode chemistry development, with manufacturers actively working to reduce dependence on cobalt. New formulations incorporating higher nickel content and alternative materials are showing promising results in both performance and cost reduction.
Additionally, the standardization of battery pack designs is gaining momentum, with manufacturers recognizing the importance of serviceability and end-of-life recycling in their design approaches.
Supply chain resilience
Supply chain security has become a top priority for EV manufacturers. Companies are establishing regional manufacturing hubs to reduce logistics costs and meet increasingly stringent local content requirements. This localization strategy extends beyond assembly to include battery production and component manufacturing, creating integrated industrial ecosystems in key markets.
Vertical integration has emerged as a crucial strategy, with manufacturers taking direct control of critical component production. This approach helps ensure supply stability and enables better quality control throughout the production process.
Companies are also investing heavily in local battery material processing facilities, reducing dependence on foreign suppliers and minimizing geopolitical risks.
Sustainability integration
Environmental considerations have moved beyond compliance to become a core driver of manufacturing decisions. Advanced closed-loop manufacturing systems are being implemented to handle battery recycling, with manufacturers taking responsibility for the entire lifecycle of their products.
This approach not only reduces environmental impact but also helps secure valuable raw materials for future production.
Carbon-neutral production facilities are becoming the new standard, with manufacturers investing heavily in renewable energy infrastructure. These facilities utilize smart energy management systems, incorporating solar, wind, and energy storage solutions to maintain consistent power supply while minimizing environmental impact.
Water recycling systems and zero-waste initiatives are being integrated into manufacturing processes, significantly reducing the environmental footprint of EV production.
Cost optimization and market strategy
Cost reduction remains crucial for achieving mass-market adoption. Manufacturers are developing simplified vehicle platforms specifically designed for EVs, moving away from adapted conventional vehicle platforms. These purpose-built platforms offer better performance, improved efficiency, and lower production costs.
Strategic partnerships are becoming increasingly important, particularly in research and development. Companies are sharing development costs for new technologies and platforms, allowing for more rapid innovation while distributing financial risk. This collaborative approach is particularly evident in software development and battery technology advancement.
Competitive landscape evolution
The market is experiencing significant restructuring as traditional automakers accelerate their transition to electric vehicles. These established players are leveraging their manufacturing expertise while adapting to new technological requirements. Simultaneously, new market entrants are introducing innovative manufacturing approaches and business models, challenging conventional industry practices.
The mid-range vehicle segment is becoming increasingly competitive, with manufacturers striving to deliver enhanced features and performance at accessible price points. Software integration and over-the-air update capabilities are becoming key differentiators, with manufacturers investing heavily in digital infrastructure and user experience development.
Looking ahead
As the industry continues to evolve, manufacturers face multiple challenges including battery material supply constraints, skilled workforce shortages and infrastructure limitations. However, these challenges are driving innovation in manufacturing processes and business models. The most successful companies will be those that can effectively balance innovation, cost optimization, and sustainability while meeting increasingly sophisticated consumer demands. Success in this rapidly evolving industry will require manufacturers to maintain flexibility in their production systems while continuously innovating in areas of battery technology, manufacturing processes, and supply chain management. The next few years will be crucial in determining which manufacturers emerge as leaders in this transformed automotive landscape.